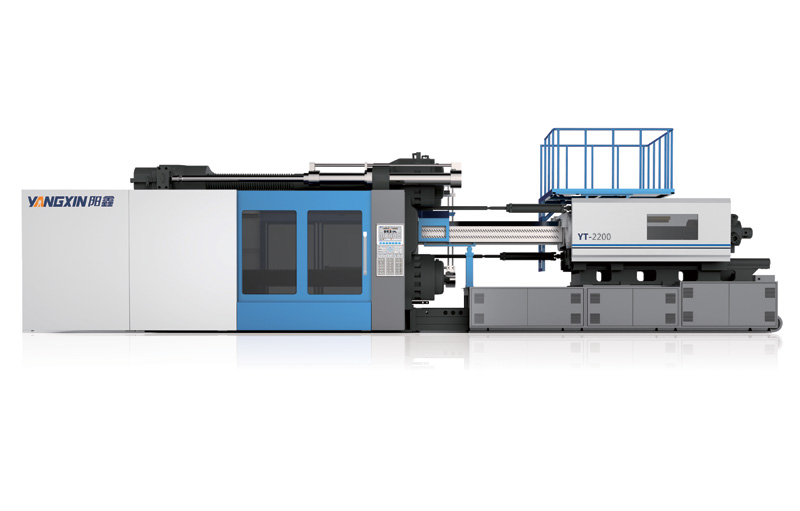
Two-plate large molding machine
Model number: YT-2200
Views:
Support hotline:86-752-6833832
Detailed description
Precise locking system, outstanding efficiency, efficient servo drive, all meet all requirements. Focus on customer products, provide a complete set of technical solutions for customers, and create better investment returns and customer experience for global customers.
With the lower cost of investment, we need to build a two plate machine with less room for production.
◆ Quickly mold open/ close hydraulic cylinder and high pressure clamping hydraulic cylinder are respective, reducing the consumption of hydraulic oil to 50%.
◆ Respective mold clamping cylinder is not integrated with the platen, as a whole, without oil leakage problem by casting sand hole.
◆ Non-mechanism mold adjustment, less fault issue.
◆ Especial design on mold open force, only use 10% compare to mold closing force.
◆ The high pressure clamping screw nut can be completely locked in the quick process to clamping the mold, then the cycle time be shorten.
◆ The moveable platen adopts linear sliding rail, which makes the motion more stable and the efficiency higher.
◆ Can increase the platen size and the space between tie bar, according co customer needs, suitable for large mold;
◆ Cooperating with customer demand to modify the various combination on injection unit and clamping unit.
◆ Respective clamping cylinder (not be casted together with stand platen), the oil seal can be replaced by whole set.
◆ The tie bar and the piston of the clamping cylinder are separated, The tie bar is not raquired to be removed when replacing the oil seal of the piston, and the cylinder is not required to be removed when replacing the tie bar.
◆ Advanced two-platen clamping mechanism, simplified equipment, compact structure, can save factory occupied space.
◆ Since the zero friction between the tie bar and the movable platen, the service life is longer. Due to the two diagonal fast movement cylinder, the opening and closing speed has been improved greatly.
◆ Synchronous pull rod brake device, adding brake cylinder with buffer function, make the brake performs accurately and smoothly.
Note: The output of this product parameter is calculated according to the specific gravity of polystyrene of 1.05, assuming an efficiency of 0.88. As the product is continuously researched and improved, the design changes are subject to change without notice.
Energy efficient, precise and fast
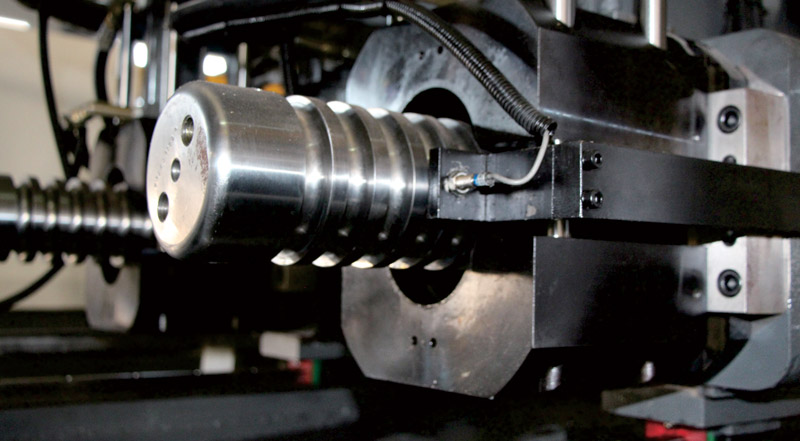
Space save
◆ The two-plate structure, shorten the length of the machine, and save 25-30% of the factory space.◆ Quickly mold open/ close hydraulic cylinder and high pressure clamping hydraulic cylinder are respective, reducing the consumption of hydraulic oil to 50%.
Mechanical more durable
◆ Mechanical more durable FEA design, box structure, less deformation of the platen.◆ Respective mold clamping cylinder is not integrated with the platen, as a whole, without oil leakage problem by casting sand hole.
◆ Non-mechanism mold adjustment, less fault issue.
◆ Especial design on mold open force, only use 10% compare to mold closing force.
More rapid production
◆ Hydraulic clamping structure of two platen type can be quicker on mold mounting and dismounting. Simultaneously process ejecting function while mold opening, save the molding cycle time. ◆ Without contact between the tie bar and clamping cylinder, the movable platen does not affect the movement of the pison.◆ The high pressure clamping screw nut can be completely locked in the quick process to clamping the mold, then the cycle time be shorten.
More precise postioning
◆ With two diagonal cylinder fast movement, and with the baxe of the movable platen support by slipper guide keep the movable platen more stable, and the mold contact more precise.◆ The moveable platen adopts linear sliding rail, which makes the motion more stable and the efficiency higher.
More flexibility
◆ In order to meet customer demand to increase the mold thickness and mold stroke, suitable for deep barrel mold.◆ Can increase the platen size and the space between tie bar, according co customer needs, suitable for large mold;
◆ Cooperating with customer demand to modify the various combination on injection unit and clamping unit.
Easy maintenance
◆ Due to the tie bar and the cylinder piston are separated, not in conatct, easy maintenance.◆ Respective clamping cylinder (not be casted together with stand platen), the oil seal can be replaced by whole set.
◆ The tie bar and the piston of the clamping cylinder are separated, The tie bar is not raquired to be removed when replacing the oil seal of the piston, and the cylinder is not required to be removed when replacing the tie bar.
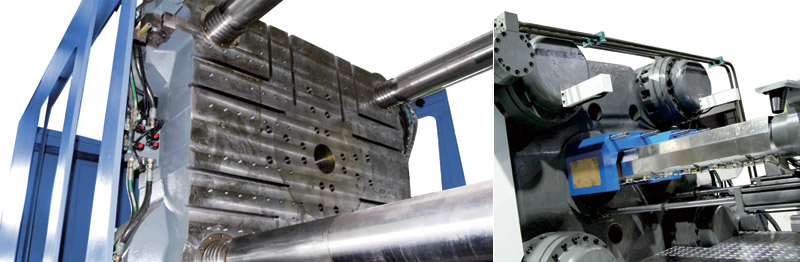
MOLD CLAMPING UNIT
Reasonable space layout, long service life◆ Advanced two-platen clamping mechanism, simplified equipment, compact structure, can save factory occupied space.
◆ Since the zero friction between the tie bar and the movable platen, the service life is longer. Due to the two diagonal fast movement cylinder, the opening and closing speed has been improved greatly.
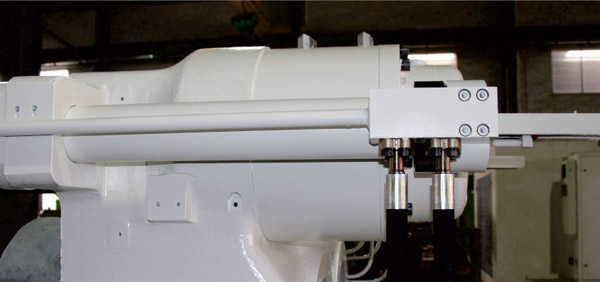
Accurate clamping
◆ Clamping pressure quick response, clasping force and main pressure are proportional, linear accurate.Pressure sensor real-time monitoring, and reproduce the hith precision of clamping force.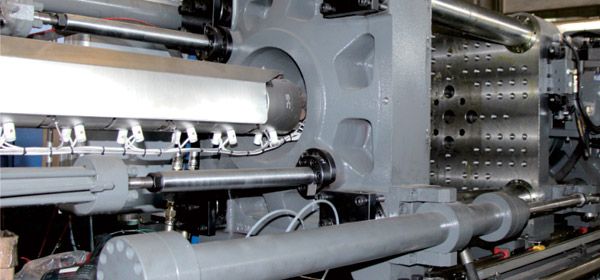
Rapid motion mechanism
◆ By diagonal located, the high speed open/ close cylinder can shorten the cycle time.◆ Synchronous pull rod brake device, adding brake cylinder with buffer function, make the brake performs accurately and smoothly.
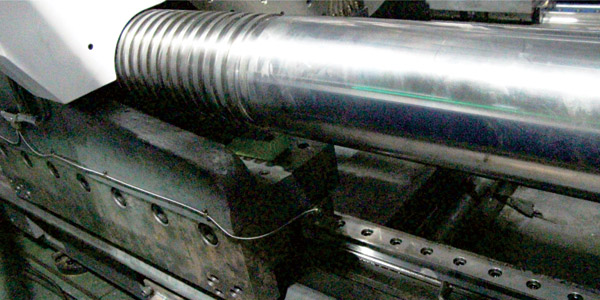
More durable slipper guide
◆ Support by slipper guide, the base of the movable platen not only ensure the precision of the production when mounting heavy molds but also improve the service ilfe of molds.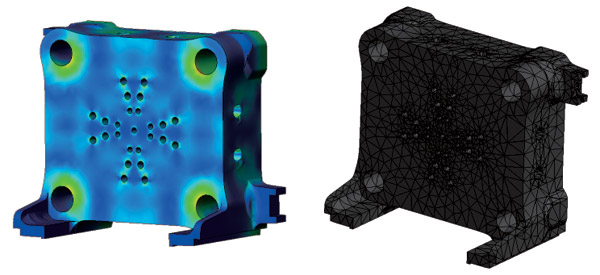
Hith rigidity plagen design
◆ Hith rigidity of the platen, uneasy to go deformation, which is beneficial to improve the life of the mold and the precision of the products.INJECTION UNIT

Fast and stable design
◆ Diagonal injection cylinder layout, the injection unit align to the center of the mold , to move smoothly;
Low pressure injection technique
◆ The mold clamping cylinder provide with compression control to perform the Injection compression function;
Hith efficiency and stable platen
◆ The lineal rail guide, at the backside of the injection unit, has the advantages on low friction, fast response and smooth movement.
High rigidity dtructure
◆ With sliding pallet, the injection unit structure has high rigidity and the center of gravity of the injection unit is more accurate for moving smoothly.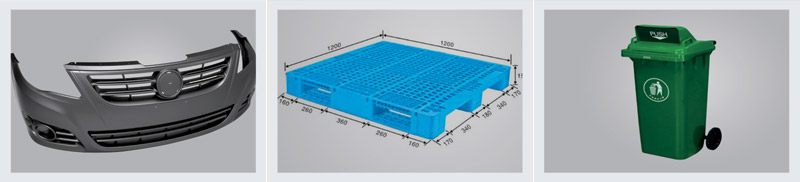
TECHNICAL PARAMETERS
Project | Unit | YT-1300 | YT-1600 | YT-1900 | YT-2200 | YT-2500 | YT-2800 | YT-3200 | YT-3700 | |||||||||
Injection Unit | Screw diameter | mm | Φ110 | Φ120 | Φ120 | Φ130 | Φ130 | Φ140 | Φ140 | Φ150 | Φ150 | Φ160 | Φ160 | Φ170 | Φ170 | Φ180 | Φ180 | Φ190 |
Theoretical shot weight | cm3 | 6411 | 7630 | 7348 | 8623 | 9486 | 11001 | 12463 | 14307 | 14660 | 16680 | 17684 | 19964 | 21212 | 23781 | 25180 | 28055 | |
Shot weight of injection (ps) | gram | 5790 | 6890 | 6635 | 7787 | 8565 | 9934 | 11254 | 13069 | 13238 | 15062 | 15969 | 18028 | 19154 | 21474 | 22737 | 25334 | |
ozs | 204.2 | 243.0 | 234.0 | 274.7 | 302.1 | 350.4 | 397.0 | 461.0 | 466.9 | 531.3 | 563.3 | 635.9 | 675.6 | 757.5 | 802.0 | 893.6 | ||
Injection pressure | kg/cm2 | 2296 | 1929 | 1856 | 1582 | 2083 | 1796 | 2061 | 1795 | 1955 | 1718 | 200 | 1773 | 1935 | 1726 | 1948 | 1748 | |
Injection rate | cm3/sec | 790 | 940 | 1052 | 1234 | 1088 | 1262 | 1100 | 1263 | 1377 | 1567 | 1472 | 1662 | 1640 | 1839 | 1760 | 1961 | |
Clamping Unit | Mould clamping force | metrictons | 1300 | 1600 | 1900 | 2200 | 2500 | 2800 | 3200 | 3700 | ||||||||
Mould clamping stroke | mm | 1510-2210 | 1750-2600 | 1750-2600 | 1850-2750 | 1950-2950 | 2250-3250 | 2200-3200 | 2300-3300 | |||||||||
Daylight Max | mm | 2860 | 3300 | 3350 | 3550 | 3750 | 4150 | 4200 | 4300 | |||||||||
Mould thickness | mm | 650-1350 | 700-1550 | 750-1600 | 800-1700 | 800-1800 | 900-1900 | 1000-2000 | 1000-2100 | |||||||||
Distance between tie bar | mm | 1350*1100 | 1550*1400 | 1660*1450 | 1850*1550 | 1950*1650 | 2050*1750 | 2200*1850 | 2300*1950 | |||||||||
Ejector stroke | mm | 300 | 300 | 350 | 350 | 400 | 400 | 450 | 450 | |||||||||
Electrical Equipment | Max. Motor power | KW | 124 | 144 | 174 | 195 | 210 | 234 | 240 | 260 | ||||||||
Temperature controller | (range)set | (0-400℃)*7 | (0-400℃)*7 | (0-400℃)*8 | (0-400℃)*8 | (0-400℃)*8 | (0-400℃)*8 | (0-400℃)*8 | (0-400℃)*8 | |||||||||
Heater power | kw | 50.6 | 53 | 75.3 | 110.6 | 115 | 121.8 | 150 | 175 | |||||||||
Others | Machine dimensions(LxWxH) | m | 10.2*3.3*2.8 | 11.3*3.5*2.9 | 13.3*3.7*3.3 | 14*4.1*3.4 | 14.3*4.2*3.5 | 14.8*4.3*3.6 | 15.3*5*3.8 | 16.5*5.3*4.1 | ||||||||
Oil tank capacity | liter | 1800 | 2300 | 2800 | 3500 | 3500 | 4000 | 4100 | 4400 | |||||||||
Machine weight | metrictons | 53 | 68 | 73 | 120 | 150 | 160 | 190 | 230 | |||||||||
System pressure | kg/cm2 | 170 | 170 | 170 | 170 | 170 | 170 | 170 | 170 |
APPEARANCE ADVANTAGE COMPARISON DIAGRAM
The advantages of flexible layout and compact size are ideal for incorporating into your production environment. | ![]() |
Note: The output of this product parameter is calculated according to the specific gravity of polystyrene of 1.05, assuming an efficiency of 0.88. As the product is continuously researched and improved, the design changes are subject to change without notice.
Next: Last pagePrevious: First page